دیسک های سنگ زنی نقشی محوری در صنایع مختلف دارند و شکل دهی و تکمیل مواد را تسهیل می کنند. با این حال، مانند هر ابزار دیگری، آنها از مسائلی که می تواند کارایی و عملکرد آنها را مختل کند مصون نیستند. در این مقاله، مشکلات رایج دیسک سنگ زنی را بررسی می کنیم، علل ریشه ای آنها را بررسی می کنیم و راه حل های موثری برای یک گردش کار یکپارچه ارائه می کنیم.
مقدمه
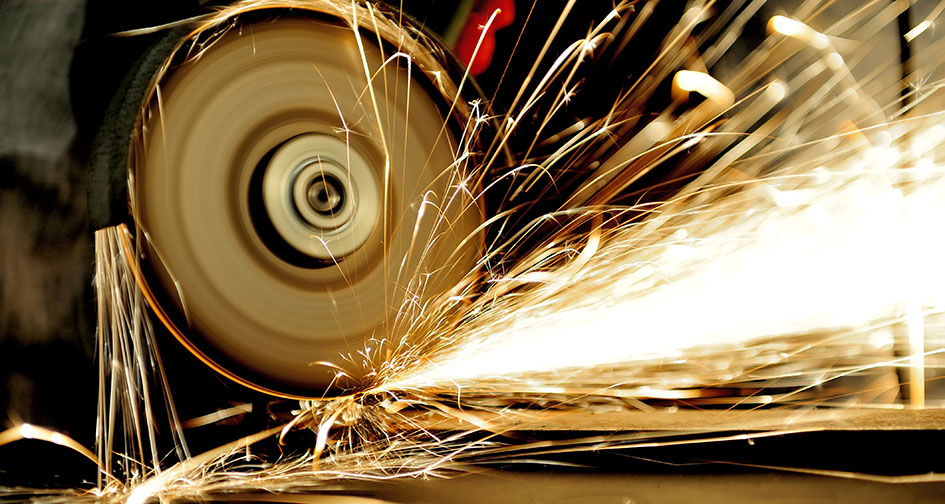
دیسک های آسیاب نقش اساسی در صنایع مختلف دارند و به عنوان ابزار ضروری برای فرآیندهای حذف مواد، شکل دادن و تکمیل هستند. درک تعریف، اهمیت آنها در صنایع، و مسائل مشترکی که با آن مواجه می شوند برای بهینه سازی استفاده از آنها و اطمینان از عملیات کارآمد بسیار مهم است.
الف. تعریف دیسک های سنگ زنی
دیسک های سنگ زنی ابزارهای ساینده ای هستند که در فرآیندهای ماشینکاری برای برش، آسیاب یا صیقل دادن سطوح مواد استفاده می شوند. این دیسکها معمولاً از ذرات ساینده تشکیل شدهاند که به یک ماده پشتی متصل میشوند و ابزار چرخشی ایجاد میکنند که میتواند مواد اضافی، سطوح صاف یا لبههای تیز را حذف کند. آنها در اشکال و اندازه های مختلف هستند که هر کدام برای کاربردهای خاصی طراحی شده اند.
ب. اهمیت در صنایع مختلف
صنعت فلزکاری:
در ساخت و تولید فلز، دیسک های سنگ زنی برای شکل دادن، جداسازی و تکمیل سطوح فلزی حیاتی هستند. آنها معمولاً برای دستیابی به ابعاد دقیق و کیفیت سطح با آسیاب های زاویه ای استفاده می شوند.
صنعت ساختمان:
متخصصان ساخت و ساز برای کارهایی مانند آماده سازی سطح بتن، صاف کردن لبه های ناهموار، و از بین بردن عیوب در موادی مانند سنگ و بتن، به دیسک های سنگ زنی متکی هستند.
صنعت خودرو:
دیسک های سنگ زنی در بخش خودرو برای کارهای مختلف از ابزارهای تیز کردن تا شکل دادن و تکمیل اجزای فلزی ضروری هستند. آنها به دقت و کیفیت قطعات خودرو کمک می کنند.
صنعت نجاری:
کارگران چوب از دیسک های آسیاب برای شکل دادن و صاف کردن سطوح چوبی استفاده می کنند. این دیسک ها در حذف مواد اضافی، اصلاح اشکال و آماده سازی چوب برای تکمیل بیشتر موثر هستند.
تولید عمومی:
دیسک های سنگ زنی در فرآیندهای مختلف تولید کاربرد پیدا می کنند که در آن حذف دقیق مواد مورد نیاز است و به تولید قطعات با کیفیت کمک می کند.
ج. مسائل رایجی که با آن روبرو هستیم
سایش و سایش دیسک:
استفاده مداوم می تواند منجر به سایش و سایش دیسک سنگ زنی شود که بر عملکرد آن تأثیر می گذارد. بازرسی و تعویض منظم برای حفظ کارایی ضروری است.
گرمای بیش از حد:
اصطکاک بیش از حد در طول استفاده طولانی مدت ممکن است منجر به گرم شدن بیش از حد شود که بر دوام دیسک و کیفیت سطح تمام شده تأثیر می گذارد. اقدامات خنک کننده مناسب و استراحت های دوره ای ضروری است.
گرفتگی:
دیسک های آسیاب می توانند بقایای مواد را جمع کنند و کارایی آنها را کاهش دهند. تمیز کردن منظم یا انتخاب دیسک هایی با ویژگی های ضد گرفتگی به جلوگیری از این مشکل کمک می کند.
لرزش و لرزش:
عدم تعادل یا سایش ناهموار ممکن است منجر به لرزش یا لرزش شود و بر کیفیت پرداخت و ایمنی عملیات تأثیر بگذارد. نصب و تعادل مناسب بسیار مهم است.
انتخاب دیسک نادرست:
انتخاب نامناسب دیسک سنگ زنی برای یک ماده یا کاربرد خاص می تواند منجر به ناکارآمدی و آسیب احتمالی شود. انتخاب مناسب بر اساس سازگاری مواد ضروری است.
درک تعریف، اهمیت و چالش های بالقوه مرتبط با دیسک های آسیاب برای صنایعی که به این ابزارها تکیه می کنند ضروری است. با پرداختن به مسائل رایج و اطمینان از استفاده مناسب، صنایع می توانند اثربخشی دیسک های آسیاب را در کاربردهای مربوطه خود به حداکثر برسانند.
ساییدگی و پارگی روی دیسک های آسیاب
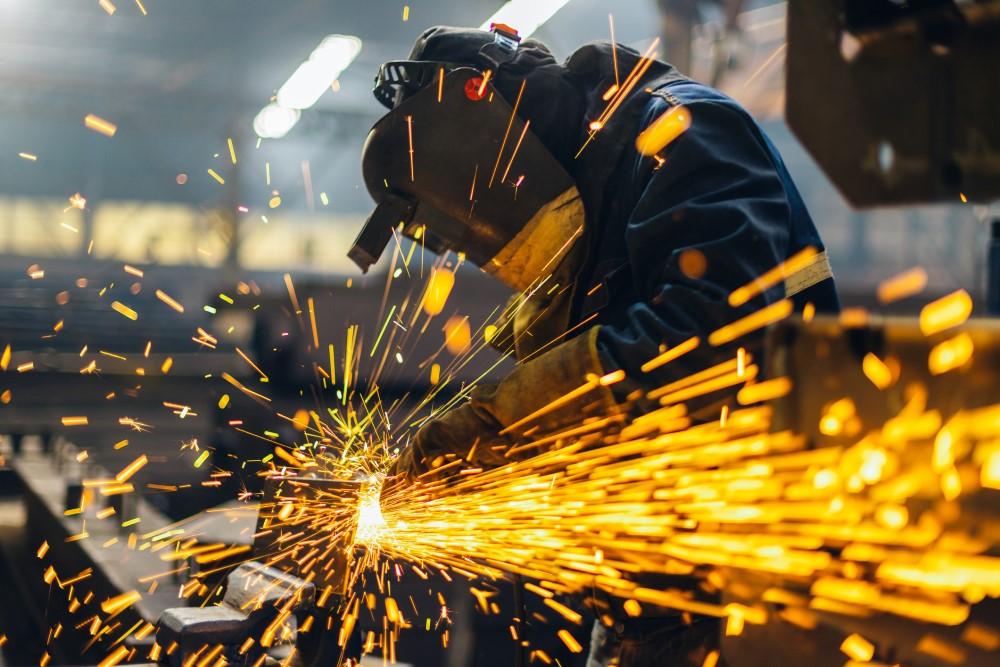
دیسک های سنگ زنی ابزار ضروری در صنایع مختلف هستند که سایش لازم را برای کارهای مختلف از ساخت فلز تا پرداخت بتن فراهم می کنند. درک عوامل موثر در سایش و پارگی دیسکهای آسیاب برای بهینهسازی عملکرد آنها و اطمینان از ایمنی بسیار مهم است.
سختی و ترکیب مواد:
تنوع سختی:دیسک های سنگ زنی با موادی با سطوح سختی متفاوت مواجه می شوند. مواد ساینده مانند فلز و بتن می توانند به طور قابل توجهی از نظر سختی متفاوت باشند. سنگ زنی مداوم در برابر مواد سخت سایش را تسریع می کند.
ترکیب مواد:وجود عناصر ساینده در ماده ای که آسیاب می شود می تواند بر سایش دیسک سنگ زنی تأثیر بگذارد. ذرات ساینده می توانند فرسودگی دیسک را تسریع کنند.
فشار و نیروی سنگ زنی:
فشار بیش از حد:اعمال فشار بیش از حد بر روی دیسک سنگ زنی می تواند منجر به سایش سریعتر شود. برای جلوگیری از فشار غیرضروری روی دیسک، استفاده از فشار توصیه شده برای کاربرد خاص ضروری است.
نیروی ناکافی: از سوی دیگر، نیروی ناکافی ممکن است منجر به سنگ زنی طولانی مدت، ایجاد اصطکاک و گرمای اضافی، و در نتیجه سایش شود.
کیفیت و ترکیب دیسک:
کیفیت مواد ساینده:کیفیت مواد ساینده مورد استفاده در دیسک سنگ زنی به طور قابل توجهی بر طول عمر آن تأثیر می گذارد. مواد ساینده با کیفیت بالا تمایل به مقاومت در برابر سایش و حفظ وضوح بیشتری دارند.
عامل پیوند:عامل پیوندی که ذرات ساینده را در کنار هم نگه می دارد نقش مهمی ایفا می کند. یک عامل اتصال دهنده با طراحی خوب، دوام دیسک را افزایش می دهد.
شرایط محیط کار:
دما:دمای بالا که در حین سنگ زنی ایجاد می شود می تواند بر ترکیب دیسک تأثیر بگذارد. گرمای بیش از حد عامل اتصال را ضعیف می کند و سایش را تسریع می کند.
رطوبت و آلاینده ها:قرار گرفتن در معرض رطوبت یا آلایندهها در محیط کار میتواند بر یکپارچگی دیسک آسیاب تأثیر بگذارد و منجر به سایش سریعتر شود.
تکنیک اپراتور:
تکنیک مناسب:مهارت و تکنیک اپراتور حیاتی است. استفاده نادرست، مانند سنگ زنی در زوایای نادرست یا استفاده از نیروی بیش از حد، می تواند به سایش ناهموار و کاهش طول عمر دیسک کمک کند.
بازرسی های منظم:اپراتورها باید به طور منظم دیسک سنگ زنی را برای هر گونه علائم آسیب یا سایش بازرسی کنند. دیسک هایی که فرسودگی را فراتر از یک نقطه مشخص نشان می دهند باید به سرعت تعویض شوند.
اندازه دیسک و سازگاری RPM:
سایز بندی صحیح:استفاده از اندازه دیسک صحیح برای آسیاب بسیار مهم است. دیسک هایی که اندازه نادرست دارند ممکن است به طور ناهموار فرسوده شوند یا خطرات ایمنی ایجاد کنند.
سازگاری RPM:رعایت دورهای توصیه شده در دقیقه (RPM) برای دیسک سنگ زنی عملکرد بهینه را تضمین می کند و از سایش زودرس جلوگیری می کند.
تعمیر و نگهداری منظم، رعایت شرایط عملیاتی توصیه شده، و انتخاب دیسک سنگ زنی مناسب برای کار، اقدامات ضروری برای به حداقل رساندن سایش و پارگی هستند. با درک عوامل مؤثر بر سایش، اپراتورها می توانند طول عمر و کارایی دیسک های سنگ زنی را افزایش دهند و به عملیات سنگ زنی ایمن تر و پربارتر کمک کنند.
سنگ زنی ناهموار
سنگ زنی ناهموار به وضعیتی اطلاق می شود که سطحی که آسیاب می شود به یک سطح صاف و یکدست نمی رسد. این مشکل می تواند به دلایل مختلفی ایجاد شود و بر کیفیت قطعه کار تأثیر بگذارد. در اینجا عوامل متداول موثر در سنگ زنی ناهموار و راه حل های بالقوه وجود دارد:
انتخاب چرخ سنگ زنی نادرست:
راه حل:اطمینان حاصل کنید که چرخ سنگ زنی برای موادی که آسیاب می شوند مناسب است. مواد مختلف به خواص ساینده خاصی نیاز دارند. نوع چرخ، اندازه شن و چسب مناسب را برای برنامه انتخاب کنید.
پانسمان نامناسب چرخ:
علت:چرخ سنگ زنی که به درستی پوشیده نشده باشد می تواند منجر به سایش ناهموار و برش بی اثر شود.
راه حل:چرخ سنگ زنی را مرتباً بپوشانید تا شکل خود را حفظ کرده و هرگونه زباله انباشته شده را از بین ببرید. پانسمان مناسب سطح برش ثابت را تضمین می کند.
سیال سنگ زنی یا خنک کننده ناکافی:
علت:استفاده ناکافی یا نادرست از سیال آسیاب می تواند منجر به افزایش اصطکاک و گرما شود و منجر به آسیاب ناهموار شود.
راه حل:برای دفع گرما و کاهش اصطکاک از مایع سنگ زنی یا خنک کننده مناسب استفاده کنید. خنک کاری مناسب برای دستیابی به نتایج یکنواخت ضروری است.
پارامترهای سنگ زنی نادرست:
علت:استفاده از پارامترهای سنگ زنی نادرست مانند سرعت بیش از حد، سرعت تغذیه یا عمق برش می تواند منجر به آسیاب ناهموار شود.
راه حل:پارامترهای سنگ زنی را با توجه به نیازهای مواد و کاربرد تنظیم کنید. برای تنظیمات بهینه به توصیه های سازنده مراجعه کنید.
چرخ سنگ زنی فرسوده:
علت:یک چرخ سنگ زنی فرسوده ممکن است سطح برش ثابتی را ایجاد نکند و در نتیجه سنگ زنی ناهموار باشد.
راه حل:هنگامی که چرخ سنگ زنی به پایان عمر قابل استفاده خود رسید، آن را تعویض کنید. به طور منظم چرخ را برای علائم سایش بررسی کنید.
فشار یا نرخ تغذیه نابرابر:
علت:فشار ناهموار یا نرخ تغذیه ناسازگار در طول آسیاب می تواند منجر به حذف نامنظم مواد شود.
راه حل:فشار یکنواخت اعمال کنید و نرخ تغذیه ثابت را در سراسر قطعه کار حفظ کنید. مهارت اپراتور و توجه به جزئیات بسیار مهم است.
مشکلات ماشین:
علت:مشکلات مکانیکی ماشین سنگ زنی، مانند ناهماهنگی یا مشکلات اسپیندل، می تواند منجر به سنگ زنی ناهموار شود.
راه حل:بررسی های تعمیر و نگهداری منظم را روی دستگاه سنگ زنی انجام دهید. برای اطمینان از عملکرد مناسب، هر گونه مشکل مکانیکی را سریعاً برطرف کنید.
تثبیت قطعه کار:
علت:قطعات کار ضعیف یا نامناسب می تواند منجر به سنگ زنی ناهموار شود.
راه حل:از نصب و تراز مناسب قطعه کار اطمینان حاصل کنید. آن را محکم ببندید تا از حرکت در طول فرآیند آسیاب جلوگیری کنید.
پرداختن به سنگ زنی ناهموار نیاز به ترکیبی از راه اندازی تجهیزات مناسب، پارامترهای عملیاتی صحیح و شیوه های نگهداری منظم دارد. اپراتورها باید برای شناسایی و اصلاح سریع مسائل برای دستیابی به نتایج با کیفیت بالا و ثابت در کاربردهای آسیاب آموزش ببینند. بازرسی های منظم و رعایت بهترین شیوه ها به حذف کارآمد و یکنواخت مواد در طول فرآیند سنگ زنی کمک می کند.
مشکلات گرمای بیش از حد
گرمای بیش از حد در حین سنگ زنی یک مسئله رایج است که می تواند بر عملکرد چرخ سنگ زنی و قطعه کار تأثیر بگذارد. گرمای بیش از حد می تواند منجر به مشکلات مختلفی شود، از جمله کاهش عمر چرخ، آسیب حرارتی به قطعه کار، و به طور کلی کاهش راندمان سنگ زنی. در اینجا دلایل و راه حل های بالقوه برای رسیدگی به مشکلات گرمای بیش از حد وجود دارد:
پارامترهای سنگ زنی نادرست:
علت:استفاده از پارامترهای سنگ زنی نامناسب، مانند سرعت بیش از حد، سرعت تغذیه، یا عمق برش، می تواند گرمای اضافی ایجاد کند.
راه حل:پارامترهای آسیاب را در محدوده توصیه شده تنظیم کنید. برای تنظیمات بهینه بر اساس موادی که آسیاب می شود، با دستورالعمل های سازنده مشورت کنید.
سرمایش یا روغن کاری ناکافی:
علت:استفاده ناکافی از مایع خنک کننده یا آسیاب می تواند منجر به افزایش اصطکاک و گرما شود.
راه حل:در طول فرآیند سنگ زنی از عرضه کافی مایع خنک کننده یا روان کننده اطمینان حاصل کنید. خنک کننده مناسب به دفع گرما کمک می کند و از آسیب حرارتی جلوگیری می کند.
انتخاب چرخ نادرست:
علت:انتخاب چرخ سنگ زنی با مشخصات نامناسب برای مواد در حال آسیاب می تواند منجر به گرم شدن بیش از حد شود.
راه حل:یک چرخ سنگ زنی با نوع ساینده، اندازه شن و چسب مناسب برای کاربرد خاص انتخاب کنید. تطبیق چرخ با مواد، تولید گرما را به حداقل می رساند.
مسائل مربوط به مواد قطعه کار:
علت:برخی از مواد، به ویژه آنهایی که رسانایی حرارتی ضعیفی دارند، بیشتر در معرض گرم شدن بیش از حد در هنگام آسیاب هستند.
راه حل:پارامترهای سنگ زنی را برای موادی با هدایت حرارتی کمتر تنظیم کنید. استفاده از چرخ سنگزنی تخصصی که برای مواد حساس به حرارت طراحی شده است را در نظر بگیرید.
مشکلات پانسمان چرخ:
علت:بی نظمی یا پانسمان نامناسب چرخ سنگ زنی می تواند منجر به تماس ناهموار و تجمع گرما شود.
راه حل:چرخ سنگ زنی را مرتباً بپوشانید تا شکل خود را حفظ کند و هرگونه لعاب یا زباله های انباشته شده را از بین ببرید. چرخهایی که بهدرستی پوشیده شدهاند، عملکرد آسیاب ثابت را تضمین میکنند.
تعمیر و نگهداری ناکافی ماشین:
علت:ماشینهای سنگزنی که به خوبی نگهداری نمیشوند میتوانند به مشکلات گرمای بیش از حد کمک کنند.
راه حل:تعمیر و نگهداری منظم در ماشین سنگ زنی، از جمله بررسی سیستم های خنک کننده، بازرسی تجهیزات پانسمان چرخ و اطمینان از تراز مناسب انجام دهید. هر گونه مشکل مکانیکی را به سرعت برطرف کنید.
جریان ناکافی خنک کننده چرخ:
علت:جریان ناکافی مایع خنک کننده به منطقه آسیاب می تواند منجر به کاهش اتلاف گرما شود.
راه حل:سیستم تحویل مایع خنک کننده را بررسی و بهینه کنید. اطمینان حاصل کنید که خنک کننده به طور موثر به منطقه آسیاب می رسد تا راندمان خنک کننده حفظ شود.
زمان سنگ زنی بیش از حد:
علت:جلسات آسیاب طولانی مدت بدون وقفه می تواند به ایجاد گرما کمک کند.
راه حل:سنگ زنی متناوب را اجرا کنید و برای جلوگیری از انباشت گرمای بیش از حد، اجازه دهید شکسته شود. این رویکرد به ویژه برای کارهای سنگ زنی بزرگ یا چالش برانگیز مهم است.
رسیدگی به مشکلات گرمای بیش از حد در سنگ زنی نیازمند یک رویکرد جامع شامل راه اندازی تجهیزات مناسب، پارامترهای سنگ زنی مناسب و شیوه های نگهداری منظم است. اپراتورها باید تولید گرما را در طول فرآیند سنگ زنی برای اطمینان از عملکرد بهینه، عمر طولانی ابزار و نتایج با کیفیت بالا نظارت و کنترل کنند.
نگرانی های ارتعاشی
لرزش بیش از حد در حین عملیات سنگ زنی می تواند منجر به مسائل مختلفی از جمله کاهش کیفیت سطح، افزایش سایش ابزار و آسیب احتمالی ماشین سنگ زنی شود. رسیدگی به نگرانی های ارتعاش برای دستیابی به فرآیندهای سنگ زنی دقیق و کارآمد بسیار مهم است. در اینجا دلایل و راه حل های بالقوه برای کاهش مشکلات ارتعاش وجود دارد:
سایش ناهموار چرخ:
علت:سایش نامنظم چرخ سنگ زنی می تواند منجر به تماس ناهموار با قطعه کار و ایجاد ارتعاش شود.
راه حل:چرخ سنگ زنی را به طور منظم بازرسی و لباس بپوشانید تا سطح صاف و ثابتی داشته باشید. نگهداری صحیح چرخ کمک می کند تا لرزش به حداقل برسد.
چرخ سنگ زنی نامتعادل:
علت:عدم تعادل در چرخ سنگ زنی، چه به دلیل سایش ناهموار یا نقص در ساخت، می تواند منجر به لرزش شود.
راه حل:چرخ سنگ زنی را با استفاده از متعادل کننده چرخ متعادل کنید. تعادل توزیع یکنواخت وزن را تضمین می کند و ارتعاشات را در حین کار کاهش می دهد.
کالیبراسیون ناکافی ماشین:
علت:کالیبراسیون ضعیف یا ناهماهنگی اجزای دستگاه، مانند دوک چرخ یا میز کار، می تواند به لرزش کمک کند.
راه حل:به طور منظم اجزای دستگاه را کالیبره و تراز کنید تا از عملکرد مناسب اطمینان حاصل کنید. دستورالعمل های سازنده را برای راه اندازی و تراز کردن ماشین دنبال کنید.
عدم تعادل قطعه کار:
علت:یک قطعه کار ناهموار یا نامناسب می تواند باعث عدم تعادل و ایجاد ارتعاش شود.
راه حل:قطعه کار را به درستی محکم کنید و مطمئن شوید که به طور یکنواخت در موقعیت و گیره قرار گرفته است. قبل از شروع فرآیند سنگ زنی، هرگونه مشکل عدم تعادل را برطرف کنید.
انتخاب چرخ نادرست:
علت:استفاده از چرخ سنگ زنی با مشخصات نامناسب می تواند منجر به لرزش شود.
راه حل:یک چرخ سنگ زنی با نوع ساینده، اندازه شن و چسب مناسب برای ماده ای که آسیاب می شود انتخاب کنید. تطبیق چرخ با برنامه ارتعاشات را به حداقل می رساند.
فرسودگی ماشین آلات:
علت:قطعات فرسوده یا آسیب دیده ماشین، مانند یاتاقان ها یا دوک ها، می توانند در ایجاد لرزش نقش داشته باشند.
راه حل:قطعات فرسوده دستگاه را به طور منظم بازرسی و تعویض کنید. نگهداری صحیح به جلوگیری از لرزش بیش از حد کمک می کند و عمر دستگاه سنگ زنی را افزایش می دهد.
جریان ناکافی مایع خنک کننده:
علت:جریان ناکافی مایع خنککننده به منطقه آسیاب میتواند باعث ایجاد گرما و ارتعاش شود.
راه حل:سیستم تحویل مایع خنک کننده را برای اطمینان از خنک کننده مناسب بهینه کنید. خنک کننده موثر خطر انبساط و انقباض حرارتی را کاهش می دهد که می تواند منجر به ارتعاش شود.
مشکلات نگهدارنده ابزار:
علت:مشکلات مربوط به نگهدارنده ابزار یا رابط اسپیندل می تواند باعث ایجاد ارتعاش شود.
راه حل:اطمینان حاصل کنید که نگهدارنده ابزار به طور ایمن نصب شده است و به درستی با دوک تراز شده است. برای به حداقل رساندن ارتعاشات از نگهدارنده ابزار با کیفیت بالا و نگهداری مناسب استفاده کنید.
پایه ماشین:
علت:فونداسیون ضعیف دستگاه یا پشتیبانی ناکافی می تواند ارتعاشات را تقویت کند.
راه حل:اطمینان حاصل کنید که ماشین سنگ زنی بر روی پایه ای ثابت و به درستی طراحی شده نصب شده است. برای به حداقل رساندن ارتعاشات منتقل شده به دستگاه، مشکلات ساختاری را برطرف کنید.
پرداختن موثر به نگرانی های ارتعاش در سنگ زنی نیاز به ترکیبی از نگهداری مناسب ماشین، انتخاب چرخ و جابجایی قطعه کار دارد. اپراتورها باید شیوههای بازرسی و نگهداری منظم را برای شناسایی و حل سریع مسائل اجرا کنند که در نتیجه عملکرد و کیفیت آسیاب بهبود مییابد.
مشکلات بارگیری در سنگ زنی
بارگذاری در سنگ زنی به پدیده ای اطلاق می شود که در آن فضاهای بین دانه های ساینده روی چرخ سنگ زنی با مواد در حال آسیاب پر می شود و در نتیجه باعث کاهش عمل برش و افزایش اصطکاک می شود. بارگذاری می تواند بر کارایی و کیفیت فرآیند سنگ زنی تأثیر منفی بگذارد. در اینجا دلایل و راه حل های بالقوه برای رفع مشکلات بارگذاری وجود دارد:
جنس قطعه کار نرم:
علت:آسیاب کردن مواد نرم می تواند منجر به مسدود شدن سریع دانه های ساینده شود.
راه حل:هنگام کار بر روی مواد نرم تر از چرخ سنگ زنی با شن درشت تر و ساختار باز استفاده کنید. این به جلوگیری از بارگذاری سریع کمک می کند و امکان حذف کارآمد تراشه را فراهم می کند.
آلودگی مواد:
علت:آلاینده های موجود در مواد قطعه کار، مانند روغن، گریس، یا باقی مانده های مایع خنک کننده، می توانند در بارگذاری نقش داشته باشند.
راه حل:از تمیز کردن مناسب قطعه کار قبل از آسیاب کردن برای حذف آلاینده ها اطمینان حاصل کنید. برای به حداقل رساندن بارگیری از مایعات برش یا خنک کننده مناسب استفاده کنید.
کاربرد نادرست خنک کننده:
علت:استفاده ناکافی یا نادرست مایع خنک کننده می تواند منجر به روانکاری و خنک سازی ناکافی و در نتیجه بارگیری شود.
راه حل:جریان و غلظت مایع خنک کننده را بهینه کنید. اطمینان حاصل کنید که مایع خنک کننده به طور موثر به منطقه سنگ زنی می رسد تا فرآیند روانکاری و خنک شود و از بارگذاری جلوگیری شود.
تیزی ناکافی چرخ:
علت:چرخ های سنگ زنی کسل کننده یا فرسوده بیشتر مستعد بارگیری هستند زیرا کارایی برش خود را از دست می دهند.
راه حل:چرخ سنگ زنی را مرتباً لباس بپوشید و تیز کنید تا تیزی آن حفظ شود. برای آشکار کردن دانه های ساینده تازه و افزایش عملکرد برش، از کمد چرخ دار استفاده کنید.
سرعت چرخ پایین:
علت:کارکردن چرخ سنگ زنی با سرعت کم ممکن است نیروی گریز از مرکز کافی برای بیرون راندن تراشه ها ایجاد نکند و منجر به بارگیری شود.
راه حل:اطمینان حاصل کنید که ماشین سنگ زنی با سرعت توصیه شده برای ترکیب چرخ و قطعه کار خاص کار می کند. سرعت های بالاتر می تواند به حذف بهتر تراشه کمک کند.
فشار بیش از حد:
علت:اعمال فشار بیش از حد در هنگام سنگ زنی می تواند مواد را وارد چرخ کند و باعث بارگیری شود.
راه حل:از فشار آسیاب متوسط و ثابت استفاده کنید. نرخ تغذیه را طوری تنظیم کنید که چرخ بدون فشار بیش از حد که منجر به بارگیری می شود، به طور موثر برش دهد.
مشخصات چرخ اشتباه:
علت:استفاده از چرخ سنگ زنی با مشخصات نادرست برای مواد در حال آسیاب می تواند منجر به بارگیری شود.
راه حل:یک چرخ سنگ زنی با نوع ساینده، اندازه سنگ ریزه و چسب مناسب برای کاربرد خاص انتخاب کنید. تطبیق چرخ با مواد به جلوگیری از بارگیری کمک می کند.
تمیز کردن ناکافی مایع خنک کننده:
علت:خنک کننده آلوده یا قدیمی ممکن است به مشکلات بارگیری کمک کند.
راه حل:برای جلوگیری از تجمع آلاینده ها، مایع خنک کننده را به طور مرتب تمیز و تعویض کنید. خنککننده تازه و تمیز، روانکاری و خنککاری را افزایش میدهد و احتمال بارگیری را کاهش میدهد.
تکنیک لباس پوشیدن نامناسب:
علت:پانسمان نادرست چرخ سنگ زنی می تواند منجر به بی نظمی و بارگیری شود.
راه حل:چرخ را با استفاده از ابزار پانسمان مناسب به درستی بپوشانید. برای جلوگیری از بارگیری، از ثابت بودن پروفیل چرخ و بدون بی نظمی اطمینان حاصل کنید.
پرداختن موثر به مسائل بارگیری شامل ترکیبی از انتخاب چرخ مناسب، راه اندازی ماشین و شیوه های نگهداری است. اپراتورها باید از رویه های توصیه شده پیروی کنند، از پارامترهای سنگ زنی مناسب استفاده کنند، و چرخ پانسمان منظم را برای به حداقل رساندن بارگذاری و بهینه سازی عملکرد سنگ زنی پیاده سازی کنند.
انتخاب دیسک سنگ زنی مناسب برای دستیابی به نتایج بهینه در کاربردهای مختلف فلزکاری و ساخت بسیار مهم است. انتخاب به عواملی مانند ماده مورد کار، پرداخت مورد نظر و نوع آسیاب مورد استفاده بستگی دارد.
انتخاب دیسک سنگ زنی مناسب
سازگاری مواد:
فلزات آهنی (فولاد، آهن):از دیسک های آسیاب که به طور خاص برای فلزات آهنی طراحی شده اند استفاده کنید. این دیسک ها اغلب حاوی مواد ساینده مناسب برای سختی فولاد هستند و کمتر مستعد بارگیری هستند.
فلزات غیرآهنی (آلومینیوم، برنج):برای جلوگیری از گرفتگی، دیسک هایی با مواد ساینده مناسب برای فلزات نرمتر انتخاب کنید. دیسک های اکسید آلومینیوم یا کاربید سیلیکون انتخاب های رایج هستند.
مواد ساینده:
اکسید آلومینیوم:مناسب برای سنگ زنی همه منظوره روی فلزات آهنی. بادوام و همه کاره است.
آلومینا زیرکونیا:راندمان برش و طول عمر بالاتری را ارائه می دهد و برای سنگ زنی تهاجمی بر روی فلزات آهنی و غیر آهنی مناسب است.
سیلیکون کاربید:ایده آل برای سنگ زنی فلزات و سنگ های غیر آهنی. نسبت به اکسید آلومینیوم تیزتر اما دوام کمتری دارد.
اندازه گریت:
شن درشت (24-36):حذف سریع انبار و سنگ زنی سنگین.
گریت متوسط (40-60):حذف استوک و پرداخت سطح را متعادل می کند.
ریزه ریز (80-120):یک سطح صاف را فراهم می کند، مناسب برای آماده سازی سطح و سنگ زنی سبک.
نوع چرخ:
نوع 27 (مرکز افسرده):دیسک سنگ زنی استاندارد با سطح صاف، ایده آل برای سنگ زنی سطح و کار لبه.
نوع 29 (مخروطی):طراحی زاویه دار برای حذف تهاجمی استوک و ترکیب بهتر سطح.
نوع 1 (مستقیم):برای برنامه های برش استفاده می شود. پروفیل نازکی برای برش دقیق فراهم می کند.
کاربرد:
سنگ زنی:دیسک های سنگ زنی استاندارد برای حذف و شکل دادن مواد.
برش:از چرخ های برش برای برش فلز استفاده کنید تا لبه صاف و تمیزی ایجاد کنید.
دیسک های فلپ:سنگ زنی و تکمیل را در یک ترکیب کنید. مناسب برای مخلوط کردن و صاف کردن سطوح.
سازگاری با آسیاب:
اطمینان حاصل کنید که دیسک سنگ زنی با نوع و سرعت آسیاب مورد استفاده سازگار است. توصیه های سازنده را برای حداکثر RPM (دور در دقیقه) دیسک بررسی کنید.
ویژگی وظیفه:
حذف سهام سنگین:برای حذف کارآمد مواد، یک شن درشت و یک دیسک نوع 27 یا 29 انتخاب کنید.
تکمیل سطح:برای پرداخت صافتر، دانههای متوسط تا ریز را با دیسکهای فلپ انتخاب کنید.
ملاحظات ایمنی:
از دستورالعمل های ایمنی، از جمله پوشیدن تجهیزات حفاظت فردی مناسب (PPE) مانند عینک ایمنی و دستکش پیروی کنید.
برای دوام و ایمنی بیشتر، دیسک های تقویت شده را انتخاب کنید.
برند و کیفیت:
دیسکهایی را از مارکهای معتبر که به دلیل کیفیت و ثبات شهرت دارند، انتخاب کنید. دیسک های با کیفیت بالا عملکرد و دوام بهتری را ارائه می دهند.
در نظر گرفتن هزینه:
هزینه اولیه را با طول عمر مورد انتظار و عملکرد دیسک سنگ زنی متعادل کنید. دیسک های باکیفیت ممکن است هزینه اولیه بالاتری داشته باشند، اما در طول زمان می توانند ارزش بهتری داشته باشند.
با در نظر گرفتن این عوامل، اپراتورها می توانند دیسک سنگ زنی مناسب را برای کاربردهای خاص خود انتخاب کنند و از کارایی، ایمنی و نتایج بهینه اطمینان حاصل کنند.
نتیجه گیری
در نتیجه، انتخاب دیسک سنگ زنی مناسب یک جنبه حیاتی برای دستیابی به نتایج موفق فلزکاری و ساخت است. انتخاب به عوامل مختلفی مانند مواد مورد کار، پرداخت مورد نظر و نوع آسیاب مورد استفاده بستگی دارد. با در نظر گرفتن سازگاری مواد، نوع ساینده، اندازه شن، نوع چرخ، کاربرد، سازگاری با آسیاب، ویژگی کار، ایمنی، کیفیت نام تجاری و هزینه، اپراتورها می توانند تصمیمات آگاهانه ای برای افزایش کارایی و ایمنی در فرآیندهای آسیاب خود بگیرند.
رعایت دستورالعمل های ایمنی، پوشیدن تجهیزات حفاظت فردی مناسب و پیروی از توصیه های سازنده برای سازگاری آسیاب و دیسک ضروری است. دیسک سنگ زنی مناسب چه برای حذف مواد سنگین، چه برای تکمیل سطح یا برنامه های برش، می تواند به طور قابل توجهی بر کیفیت و کارایی کار تأثیر بگذارد.
علاوه بر این، بررسیهای دورهای برای ساییدگی و پارگی، رسیدگی به مسائلی مانند نگرانیهای مربوط به گرمای بیش از حد و لرزش، و درک مشکلات بارگذاری به طولانیتر شدن عمر دیسک سنگزنی و اطمینان از عملکرد ثابت کمک میکند.
به طور خلاصه، یک رویکرد کاملاً آگاهانه و سیستماتیک برای انتخاب، استفاده و نگهداری دیسکهای آسیاب کلیدی برای دستیابی به نتایج بهینه، افزایش بهرهوری و تضمین یک محیط کاری ایمن است.
زمان ارسال: ژانویه-12-2024